Description
Introducing the X3 D1 Pliabot Aerial Inspector
1. Safe and Stable Operation
The X3 D1 Pliabot Aerial Inspector ensures safe, stable contact with surfaces during high-altitude operations. Its pliable gimbal stabilizes the drone while in flight or hover, ensuring consistent performance even during lateral contact tasks.
2. Adaptation to Complex Inspections
This system supports a wide range of sensors, making it highly adaptable for various complex inspections, including non-destructive testing, thickness detection, thermal imaging, and ultrasonic testing. The quick-change modular design facilitates fast implementation, making it versatile for many high-altitude detection tasks.
3. Seamless Integration with Drone Platforms
The X3 D1 is compatible with standard 3kg payload drones, such as the DJI M300 and M350, allowing seamless integration with flight control systems. One operator can easily control both the drone and detection platform, making operations efficient and straightforward. Additionally, customization integration with more drone platforms is possible for more diverse applications.
4. Rapid Deployment and Storage
Thanks to its quick-change modular design, the system can be deployed in under a minute, boosting operational efficiency. The compact design of the operation module, which folds into a Z-shape, makes it easy to store and transport, reducing storage space to just 0.8 meters.
5. Enhanced Detection and Force Feedback
Equipped with a high-definition camera, the system provides real-time monitoring and allows for timely adjustments. The pliable gimbal ensures stable contact during lateral operations, maintaining a continuous lateral contact force of up to 20N for 20 seconds. This guarantees that complex contact detection tasks are completed safely and accurately.
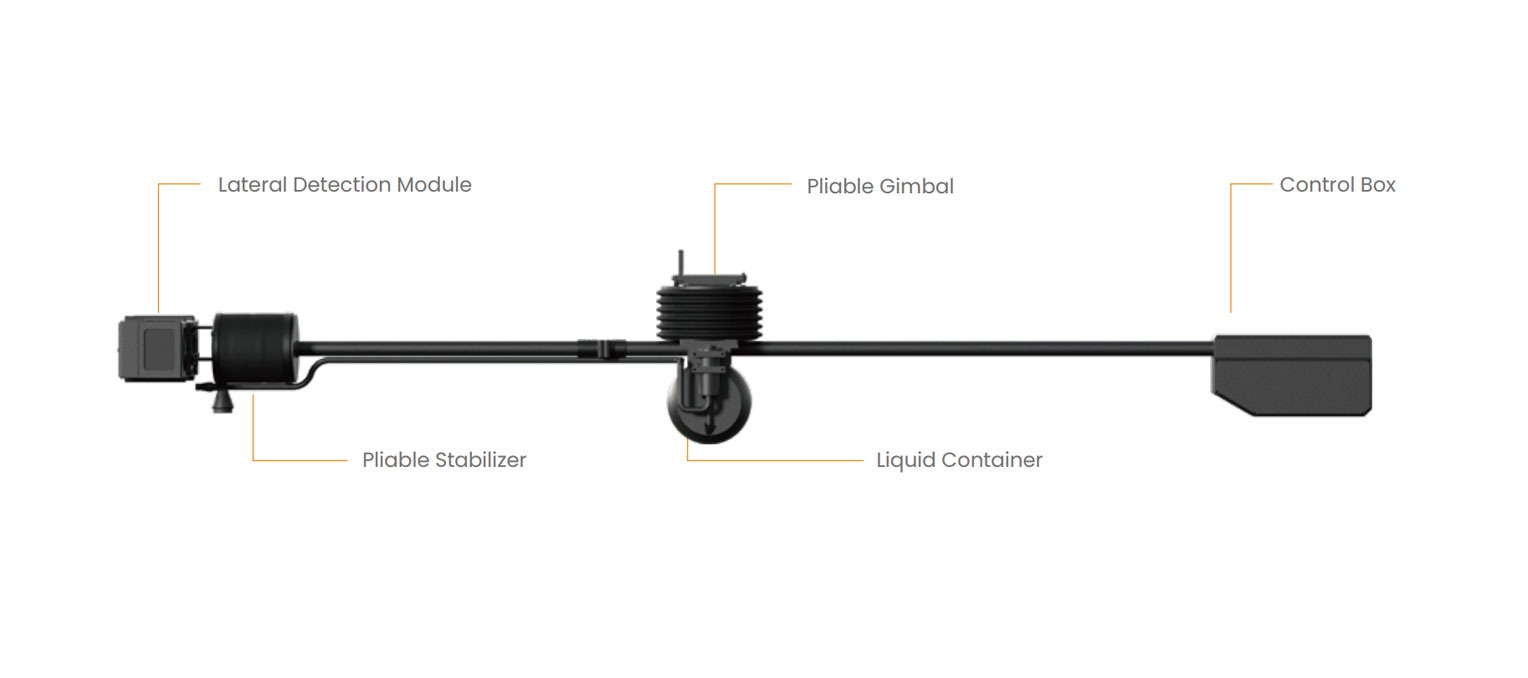
Case Study: Aerial Contact-based Concrete Strength Testing for Bridges
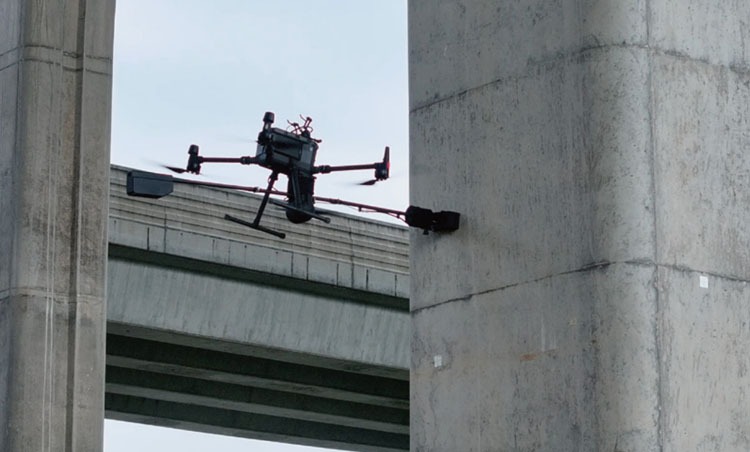
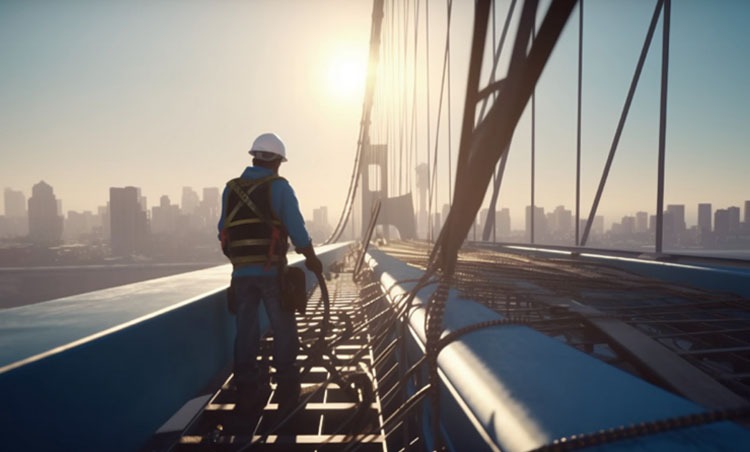
- 1. Introduction to Concrete Electrical Resistivity Testing
- To begin with, the electrical resistivity of concrete plays a crucial role in assessing the quality and long-term durability of concrete structures. Not only is this testing method essential for quality assurance, but it is also indispensable for monitoring the health of infrastructure such as buildings, roads, bridges, and offshore platforms. Therefore, conducting regular resistivity testing ensures that these structures continue to perform optimally over time. That said, the process itself often presents difficulties—especially when inspections take place in hard-to-reach or hazardous environments, such as elevated offshore bridge sites.
- 2. Challenges in Testing Concrete Electrical Resistivity
- Moving forward, it’s important to understand the challenges associated with concrete resistivity testing. First and foremost, the procedure is inherently complex and frequently poses safety concerns. Traditional testing methods typically require personnel to access remote or dangerous areas, which significantly increases risk. Furthermore, the equipment used in these methods tends to be bulky and time-consuming to set up. As a result, the testing process becomes not only labor-intensive but also vulnerable to human error—factors that collectively increase both operational costs and the potential for inaccurate data.
- 3. Safety and Operational Efficiency: The Role of Remote Control
- Fortunately, advancements in modern technology have revolutionized this process. By incorporating remote-controlled systems, just one operator can manage the entire procedure from a safe location. This game-changing capability eliminates the need for physical presence in risky or elevated environments. Consequently, safety risks decrease substantially, while operational efficiency skyrockets. In other words, remote control doesn’t just make testing safer—it makes it smarter and faster as well.
- 4. Simplified Process Through Innovative Design
- Moreover, the innovation doesn’t stop at remote control. The X3-D1 robot comes equipped with a built-in humidifier, effectively removing the need to pre-wet surfaces before testing. In contrast to conventional methods that include this extra step, the X3-D1 simplifies and accelerates the entire resistivity detection process. This design not only enhances workflow efficiency but also improves the speed and precision of the readings.
- 5. Easy Setup and Transport
- In addition, the X3-D1—powered by Pliabot® Technology—features a lightweight and highly adaptable structure. Thanks to this design, users can easily deploy and transport the robot, even in environments that are typically difficult to navigate. As a result, the setup process becomes faster and far less labor-intensive. Whether used in urban infrastructure or remote inspection zones, the X3-D1 offers a seamless and user-friendly experience.
- 6. Cost and Error Reduction
- Finally, by replacing manual testing methods with advanced robotics, the X3-D1 significantly reduces both labor costs and the margin for error. This advantage becomes even more evident in large-scale inspections where multiple testing points must be handled efficiently. Because the robot automates much of the process, it minimizes the need for human intervention, thereby cutting operational costs and improving overall testing reliability. Ultimately, this leads to more consistent, accurate, and economical concrete resistivity assessments.
Specifications
Items | Number of Joints | Max. Carrying Weight | Camera Pixel | Weight | IP Rating | Operating Noise | Package Dimensions | Package Weight |
---|---|---|---|---|---|---|---|---|
Spec 1 | N/A | 350 g / 0.77 lbs | 720p | N/A | N/A | N/A | N/A | N/A |
Spec 2 | N/A | 2 kg / 4.41 lbs | N/A | 2 kg / 4.41 lbs | IP54 | <80dB | 0.690.3550.365 m³ (2.26 × 1.16 × 1.20 ft³) | 12.2 kg / 26.90 lbs |
FAQ's
1. What is concrete electrical resistivity testing?
It measures how well concrete resists electrical flow, indicating its quality and durability, essential for infrastructure projects.
2. What challenges come with traditional resistivity testing?
It’s complex, requires access to dangerous locations, and is prone to human error, increasing safety risks and costs.
3. How does remote control improve safety and efficiency?
One operator can control the test remotely, reducing the need for personnel in risky areas and speeding up the process.
4. What does the built-in humidifier do?
It removes the need to pre-wet surfaces, simplifying and speeding up the testing process.
5. How does the X3-D1 robot reduce costs and errors?
It automates testing, cutting labor costs and minimizing human error, making the process faster and more accurate.
There are no reviews yet.